The Lumber Supply Chain is Going Against The Grain!
- beatricek1
- Mar 4, 2022
- 5 min read
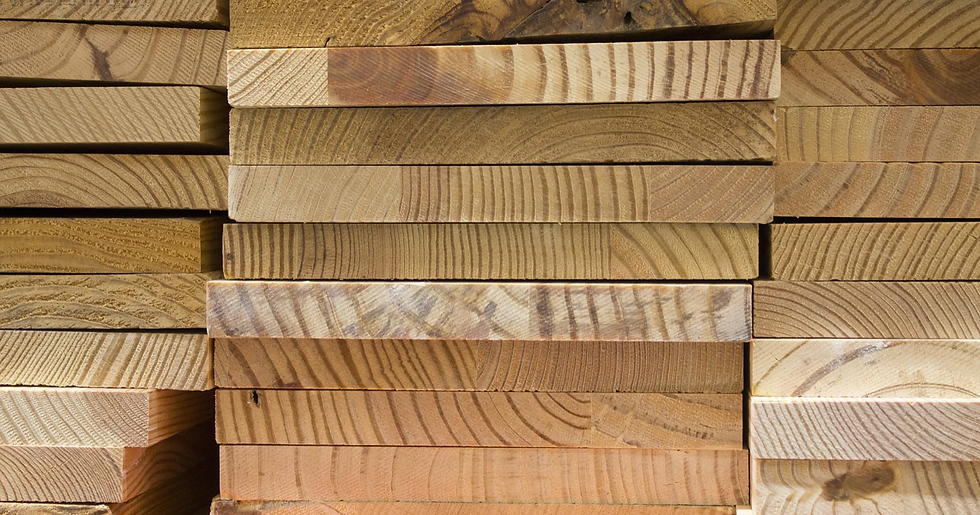
Lumber Markets: working against two closing walls
The price of lumber has increased so much, it has gone beyond the level of affordability for a lot of people. At the end of 2020, renovation businesses benefitted the most from the pandemic. With so many people working from, and staying at, home, they were more inclined to spend their money on home renovations.
Did the pandemic drive such a spike in demand that supply couldn’t keep up, forcing prices to increase? That would be one side of a very tall wall.
“Lumber extended losses to trade below $820 per thousand board feet, the lowest level since January and moving further away from an all-time high of almost $1,700 hit on May 7th as demand continues to slow while sawmills invest to increase output. Vaccinated Americans started to travel, book holidays, and engage in activities that were restricted by the pandemic, instead of spending on home renovations and DIY work.
Also, higher building costs and a declining availability of wood are starting to weigh on the market and slowing the strong pace of homebuilding. That is the wall on the opposite side. Although supply-chain disruptions persist and very few new mills are built, the rapid decline in lumber prices from mid-May suggests a bubble has burst. Still, the housing deficit in the US hints construction will remain a bright spot in the coming years, with prices of lumber remaining above pre-pandemic levels for some time.”
Lumber pricing (USD/1000 board fee) over the last 5 years is shown by tradingeconomics.com as follows:
Clearly, there has been a spike from a low in April 2020 rising in September 2020, and then taking off to a peak in May 2021. Lumber prices are up over 400% from May 2020 to May 2021. With vaccine deployment so far in advance of last year, when there was no vaccine, and life starting to get back to “normal”, why would there be such a huge increase in pricing now?

Base Raw Materials: Supply and Demand
As with many other materials, the pandemic has had the most remarkable impact on demand for, and the availability of lumber.
Supply Side Impacts
There were already issues with mill closures due to high costs, prior to the measures brought about due to the pandemic. Those closures cut industry production capacity and output prior to the onset of the pandemic.
When the pandemic began lockdowns were put in place all around the world. The impact of these lockdowns was that factories and mills were closed (in whole or in part), restricting the amount of supply. Employees were either forced to stay at home due to work stoppages, social distancing measures, infections, and quarantine mandates. Output capacity and productivity were severely reduced.
On top of that several other factors conspired to limit supply before and during the pandemic:
Wildfires in the Pacific Northwest
Mountain pine beetle infestations
U.S tariffs on the importation of softwood lumber from Canada
Annual Allowable Cut reductions in British Columbia
Being able to harvest and cut the lumber is only a part of the story. Those logs and lumber must be moved through the Supply Chain as well. That brings up the further supply impacts caused by logistics and transportation dynamics.
There are not enough truck drivers and heavy equipment to move all these goods. Lockdown and social distancing measures have impacted this area, as well as an insufficient resource to move the greater demand for goods.

Demand Side Impacts
With many people forced to stay at home for an extended period, with limited options for activities or movement outside the home, they turned to doing home renovations, creating a spike in demand at the same time that there was a contraction of supply.
In Canada and the U.S., the housing market has been white-hot, further fueled by consistently low-interest rates. This demand for new (and resale) homes has driven up pricing significantly, a function of high demand, short supply, and higher construction costs.
People who are now working from home, on a regular basis for the foreseeable future, are more inclined to:
look for new housing
start home renovation activity for home offices and other projects
As confirmation that home renovations and construction were up, in May, 2021 Home Depot reported first-quarter 2021 sales 32.7% higher than the first quarter of 2020. As stated in their quarterly investors call, “at the end of the first quarter last year, a sheet of 7/16” OSB was approximately $9.55. As we exited the first quarter this year, that same sheet of OSB more than quadrupled in price to $39.76.”
Pricing Impacts
In consideration of all of these factors contributing to short supply and strong demand, prices have increased substantially, as we’ve indicated earlier. While market pricing, as of June 2021, seems to have peaked in May, 2021, it is still substantially higher than a year ago.

Many other factors suggest that pricing should be dropping further.
Significant vaccine deployment means that very high percentages of the population have had at least one dose of the vaccine, if not two, in the U.S. and Canada. Concurrent with vaccine deployment rates more jurisdictions are relaxing pandemic-related restrictions and lockdowns. People are starting to get back to more normal activities, which will only increase further, meaning they are less focused on doing those home renovations.
Higher vaccination rates also mean that more employees will be able to go back to work. This will bring more mill throughput back online as well as more truck driver capacity.
The dramatic price increases have also raised the specter of affordability. New home construction costs alone are tens of thousands of dollars higher at current price levels. Many people were already feeling income impacts due to the pandemic. So when the latest costs of those desired renovations is considered many of these projects are cost-prohibitive. The result is that many people are waiting until prices come down to some lower level.
Even if someone wants to start their project, despite the high pricing, there is still not enough supply in the market. As such they are forced to wait it out, meaning that they are not buying now. This curtailment of demand, due to lack of supply, should also contribute to downward price pressure going forward.
Conclusion
The pandemic has been indiscriminate as to which Supply Chains it has impacted. From toilet paper to healthcare supplies (e.g. masks) to fireworks to lumber, virtually nothing has been untouched by the Coronavirus.
The lumber market dynamics are very interesting. Who would have thought that the lumber Supply Chain would be so volatile, and not just the type of commodity that we mostly ignore? It is most likely that lumber pricing will settle down to some more affordable level, though not necessarily to the pre-pandemic lows that we were used to.
Then again, until supply catches up to demand the environment still exists for extended, strong pricing. The continued rise in pricing from 2020, when we were deep in the middle of the pandemic, to peak in May 2021, when we are starting to emerge from the pandemic, suggests that we are still a way off from supply and demand coming back into a balanced state.
The overall lesson is that ANY Supply Chain is vulnerable to natural, or man-made, disasters and events. It is critical to creating as much resiliency in your Supply Chain as possible, no matter what industry you are in.
All these factors can contribute to lowering the walls blocking demand and creating more market-driven price increase resistance. Managing supply chain strategies to avoid these pitfalls in the future may help to remove those walls once and for all.
Comments