The real cost of losing our forests
- beatricek1
- Mar 3, 2022
- 6 min read
How to Manage logistics and the Lumber Supply Shortage!
There are new concerns about increasing limits on the number of trees cut down before putting our environment at risk.
Everyone from builders, manufacturers, shipping suppliers, pallet suppliers, and logistics planners is looking for alternative sources for natural materials that are readily available elsewhere.

Lumber Supply and the chain reaction to price increases
The construction of light-frame homes requires a particular type of lumber. Examples include spruce, pine, and fir trees in the United States.
When these trees are cut down, they release CO2 into our environment, adding to climate change. Additionally, the sap from these trees acts as a natural repellent against insects.
“Unfortunately, that’s not an economically viable option for us right now,” says John Deely, professor of economics at the University of Denver. A lot of companies either don’t have another market to go to, or they can’t afford to pay more than what selling into this market is paying them. This lumber shortage has led to prices in the United States rising by up to 60% in some cases, making it more expensive than imported lumber.
It’s challenging to justify relying too much on them when there are a lot of many sustainable alternatives, although this is good for American companies.
What Causes It?
The problem is that the previous material used for furniture and high-end office buildings is now being used in more homes for steel and concrete as a replacement. However, only 550 lumber mills in the United States produce these timbers. This limited number of manufacturers has somehow caused an increase in prices and a supply shortage.
The Effects of Lumber Supply Shortage
The lumber supply shortage mainly affects the price of the resources, but it also affects manufacturers. Less quantity increases production costs, which may cause some companies to lose money in the process. When this happens, they are forced to shut down their businesses.
Even after mills make more of these timbers available for construction, builders will most likely have to wait long before they can get their hands on some.
Additionally, the construction industry is still having difficulty overcoming the economic instability of the past few years. In some areas, contractors accept fewer jobs and complete them slower.

How To Mitigate The Lumber Supply Shortage?
New methods for producing highly-accurate cut timbers are being developed by saw system companies such as https://ptmi.net to help solve the shortage.
While not perfected yet, below are some ideas that will be useful to help alleviate the issue:
1. Begin Using Reclaimed Woods
The price of timber has risen drastically in the past 15 years. While this may not be a problem for large-scale companies, it’s difficult for smaller businesses to maintain.
Reclaimed wood can be found within old barns and warehouses that have been destroyed or renovated. This material should work the same way as natural lumber since its chemical makeup hasn’t changed. The only difference could be that it smells like old hay or has an extra nail dating to a few years back, but this should not affect its structural integrity.
Consider how much of a new timber would have cut down to make the reclaimed wood you are using to help protect the environment. It is a win-win situation for everyone involved if someone can use an old board instead of a newly-cut one.
2. Replacing Lumber with Alternative Materials
Perhaps, there are additional building materials used in place of wood, such as:
Metal Beams
The amount of time it takes to produce them is much longer than for timber, but they can be cheaper in the long run.
Concrete
This option may not be as aesthetically pleasing, but it can possess equal strength at a lower cost.
Fiberglass
It is very light, strong, and flexible but more expensive than other materials.
Regular Brick Or Stone
Possibly used if strength is not an issue, but both are heavy.
There are plentiful options available to anyone building or repairing something. It would be in the best interest of everyone if non-timber resources frequently were more explored.

3. Upgrading Lumber Mills
Most of the problems in the lumber industry caused by mills couldn’t keep up with the demand for certain types of timber. Mainly, it is because they weren’t using newer technology to make more boards faster. Companies are creating small-scale lumber that helps increase the overall factory output. While the ideal situation is for everyone to access these high-efficiency mills, it may not be possible given the high cost of building one.
For now, upgrading what already exists should be a priority in the lumber industry. Lumber is used throughout the world; everyone needs to find a solution soon.
4. Using Smaller Board Footages
When using smaller board footage, the order for the project doesn’t need to be changed. Instead of having a two-inch by six-inch board, install one 1 ½ inch by five inches. It will reduce the amount of wood needed while still providing the necessary support.
Technical lumber sizes are used in place of traditional ones because the names are easier to remember. The board footage may need to be adjusted, but it should not make a drastic change in the support system of whatever is being built.
5. Manufacturing Custom-Tailored Boards
One way to better utilize the lumber supply in a plant is by creating boards with custom widths and lengths. It will allow shorter pieces to be together placed, saving more wood in the long run.
For example, an eight-foot piece of timber needs to build two, two-foot pieces and one six-foot piece to complete the task. It means that a total of three full board feet in the system, while an eight-foot board only has two.
A little bit goes a long mile for this option, but companies, wisely, need to plan if they want it to pay off.
6. Employing Lumber Recycling
Plant and animal by-products aren’t the only things that can be recycled to create new products: timber is also one of them.
To help ensure that companies are properly doing their part, make sure they have recycling bins near their equipment. They should focus on using as much of a board as possible before throwing it away.
It could be due to small pieces being stuck in saws or imperfections being found on the exterior of aboard. Instead of wasting what is left, have recyclable items separated for reuse later down the line.
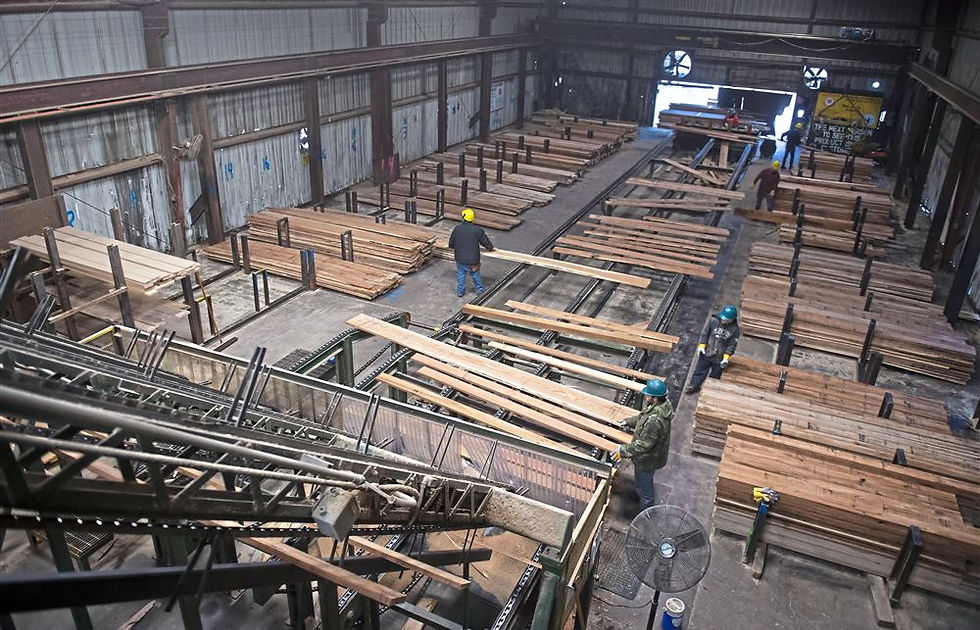
7. Increase Lumber Yield
Some sawmills are experimenting with new ways to get more lumber from a log. By making slight adjustments in the rolling and drying process, it’s possible that up to 10 percent more material can be reclaimed from each tree. While this won’t solve the problem completely, it would help alleviate some of the pressure from the current shortfall of wood.
For those trying to get ahead of the curve, investing in technology that makes more lumber per tree is a great way to get started. However, for it to work properly, everyone must be on board and follow through with future orders.
8. Taking Advantage of Plant-Based Compounds
Scientists today are constantly looking for new ways to create everything from plastics to fabrics that don’t require hemp or cotton. Some companies have already started using these materials in their products, making them more eco-friendly than ever before.
It doesn’t just stop there; another solution is using plant-based compounds when making fiberboards and particle boards. While this method reduces the amount of material needed, it also leads to a greater chance of developing cancer.
Despite those risks, companies may want to consider making this switch as soon as possible before the cost outweighs any potential benefits.
9. Forging New Deals With Lumber Producers
Another way to ensure that it has enough produced wood to meet its company’s needs is by making a few contracts with different lumber producers. It may cost more upfront, but it will ensure that everything needed for production can obtain without interruption or delay.
Once companies have this guarantee in place, they are less likely to fall behind on orders and slow down any progress in their day-to-day activities.
It can be a lot of work, and it is worth the effort and frustration when demand starts to pour in after the project is complete.
10. Working With Other Industries To Find Creative Solutions
No one knows how long the lumber supply shortage will last, but that doesn’t mean there are no other options for getting by in the meantime. One way to get through it is by working with other industries in a similar situation and might have solutions that could be useful.
For example, one company may not produce enough plywood while another struggles to make enough boxes. There may be a way to meet both of their needs by either splitting the order or combining forces. They come together and discuss what each other needs.
In Summary
Companies need to do everything they can to find a way around the lack of lumber. Whether with technology, outsourcing, or coming up with innovative methods on their own, some solutions will help the lumber industry get through this difficult time.
If these companies stay committed and searching new ways to maximize efficiency and output, they should make it through most of the shortages without any huge problems.
コメント